Piston Diaphragm Pumps
Joseph Emmerich Company
Emmerich Piston Membrane Pump – Tradition & Innovation
Piston membrane pumps are our business. Our only business! We make them Robust & Tough! Josef Emmerich founded the company in 1945 and still today the company is privately owned with a manufacturing facility composed of meticulous craftsmen. Exactly as you would expect from Germany.
Our applications of focus are a challenge to most all other reputable pump companies: Abrasive slurries at high pressure, corrosive materials, filter press feed, spray dryer feed, ore transfer, mining/tailings, cement, red mud, viscous slurries with high solids content. Our products are also tailored for the food and beverage markets.

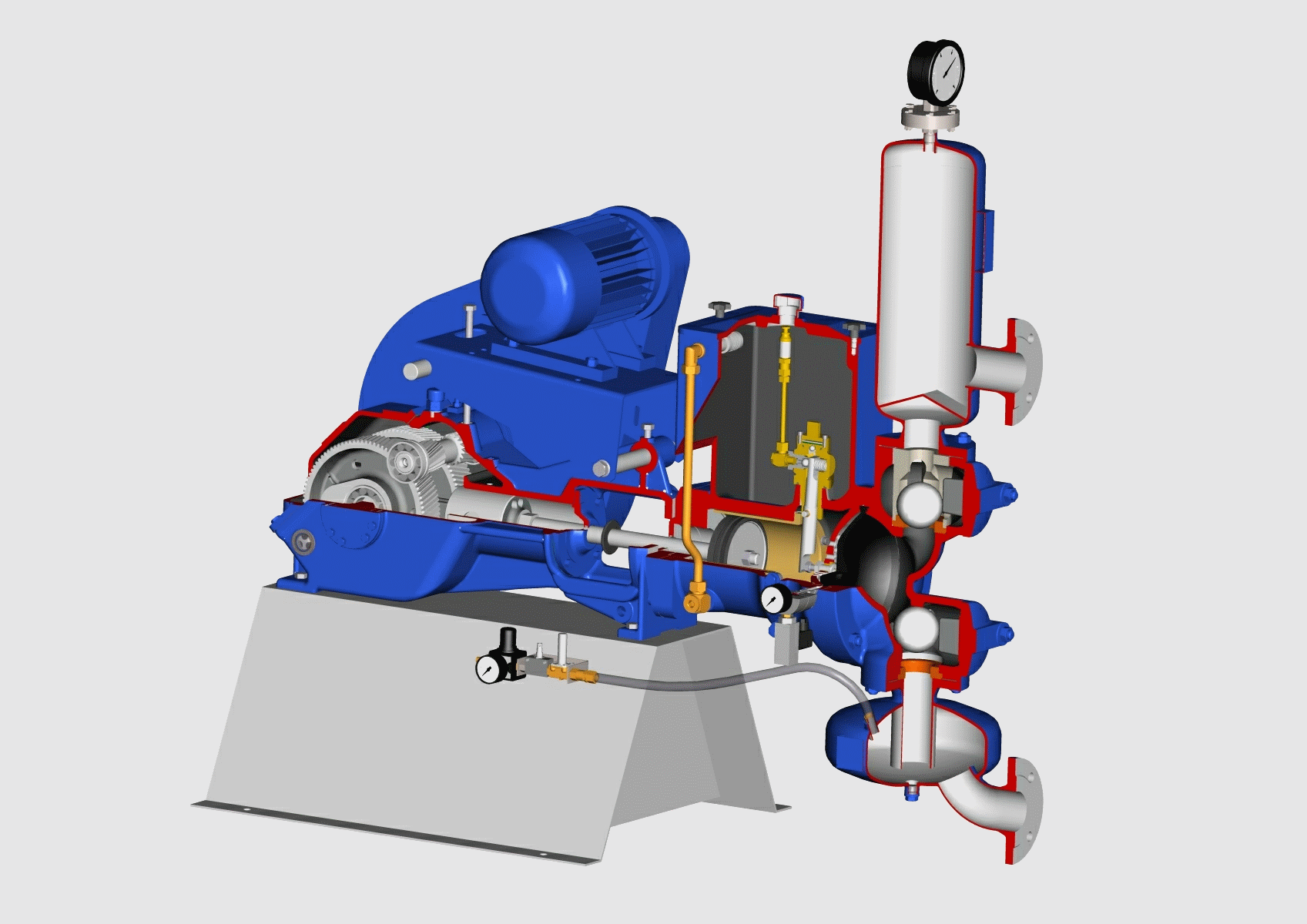
Slurry Pumping Applications
Click Here For a More Complete List
- Abrasive/Aggressive
- Acid Pump
- Beverage Pumping
- Chemical Pump
- Clay Pump
- Ceramics Pump
- Coal Gasification
- Coal Slurry
- Delicate Shear Sensitive Pump
- Energy & Power Plants
- Feedstock Pump
- Filter Press Feed Pump
- Food Products Pump
- Fly Ash Slurry
- Gasifier Feeding
- High Pressure Pump
- High Solids Pump
- High Viscosity Pump
- Kaolin Pump
- Mining/Ore Pump
- Sludge Transfer Pump
- Slurry Transfer Pump
- Spray Dryer Feed Pump
- Steel Works
- Tailings: coal, Ore
- Wine Pump
Available Emmerich Pump Models & Specifications:
Click on the Model for more info.
Model (Click For Info) | Flow Range | Pressure Range | Wet End Material | Selection Basis |
---|---|---|---|---|
0.5-65m3/hr 2.2-286 gpm | 16 bar 232 psi | Cast Iron Rubber Lined Stainless | Economical Abrasive Corrosive | |
0.5-65 m3/hr 2.2-286 gpm | 16 bar 232 psi | Polypropylene | Abrasive Corrosive | |
0.5-65 m3/hr 2.2-286 gpm | 16 bar 232 psi | Cast Iron Rubber Lined Stainless Steel | Abrasive Corrosive | |
0-65 m3/hr 0-286 gpm | 16 bar 232 psi | Polypropylene | Abrasive Corrosive | |
0.5-15 m3/hr 2.2-66 gpm | 16 bar 232 psi | Polypropylene | Abrasive Corrosive | |
0.5-400 m3/hr 2.2-1760 gpm | 250 bar 3625 psi | Cast Iron Rubber Lined Stainless Steel | Abrasive Corrosive | |
0.5-120 m3/hr 2.2-528 gpm | 16 bar 232 psi | Electrically Conductive Polypropylene | Abrasive Corrosive Explosion Proof | |
1-550 m3/hr 4.4-2420 gpm | 250 bar 3625 psi | Steel Stainless Steel | Extreme Pressure High Flow |
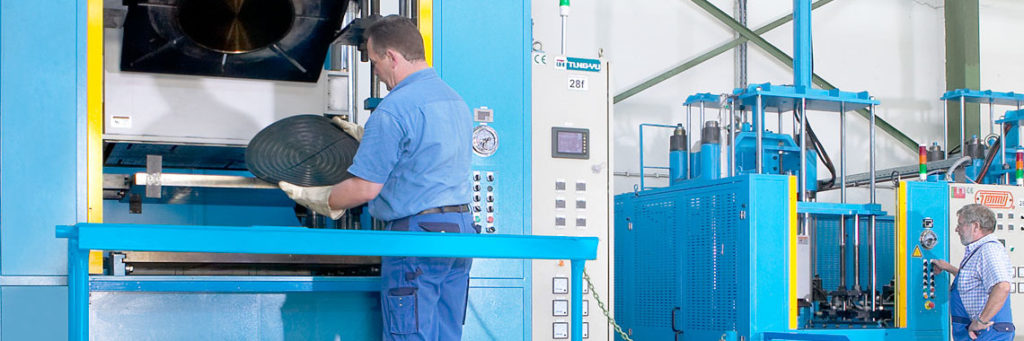
Emmerich Manufactured Pump Parts such as Multi-safe Membranes, diaphragms for diaphragm pulsation dampeners, valve seats, sealing rings, etc. are made from a wide variety of materials such as Perbunan (NBR), Neoprene (CR), Hypalon (CSM), Viton (FPM) and Vulkollan (AU).Since 1975, JOSEF EMMERICH PUMPENFABRIK GmbH has had its own in-house production of rubber parts.
Benefits:
- customized orders
- lower costs
- experience and know-how
- prompt delivery
After production, the products are properly stored in conformity with ISO 2230 in a climate-controlled room, and are available for delivery at any time.
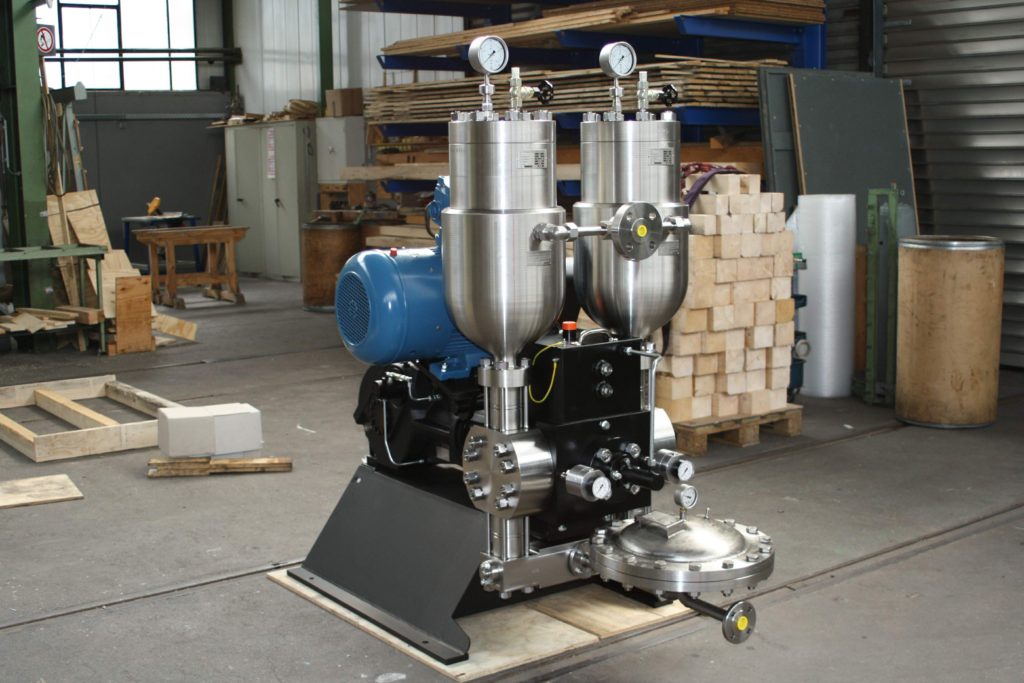
Spray Dryer Feed Pump
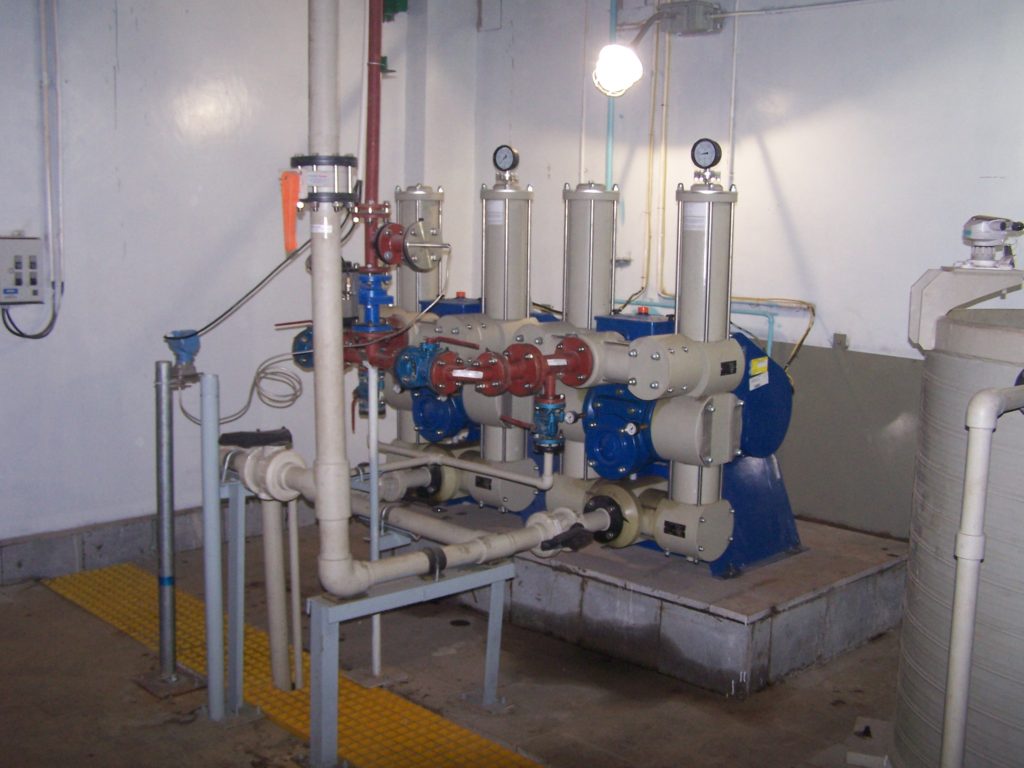
Type ER510SPPH, 1 cylinder, double acting, 8 m³/h (35 gpm), 16 bar (232 psi), Filter Press Feeding
Hydroxide sludge in galvanizing plant / Germany
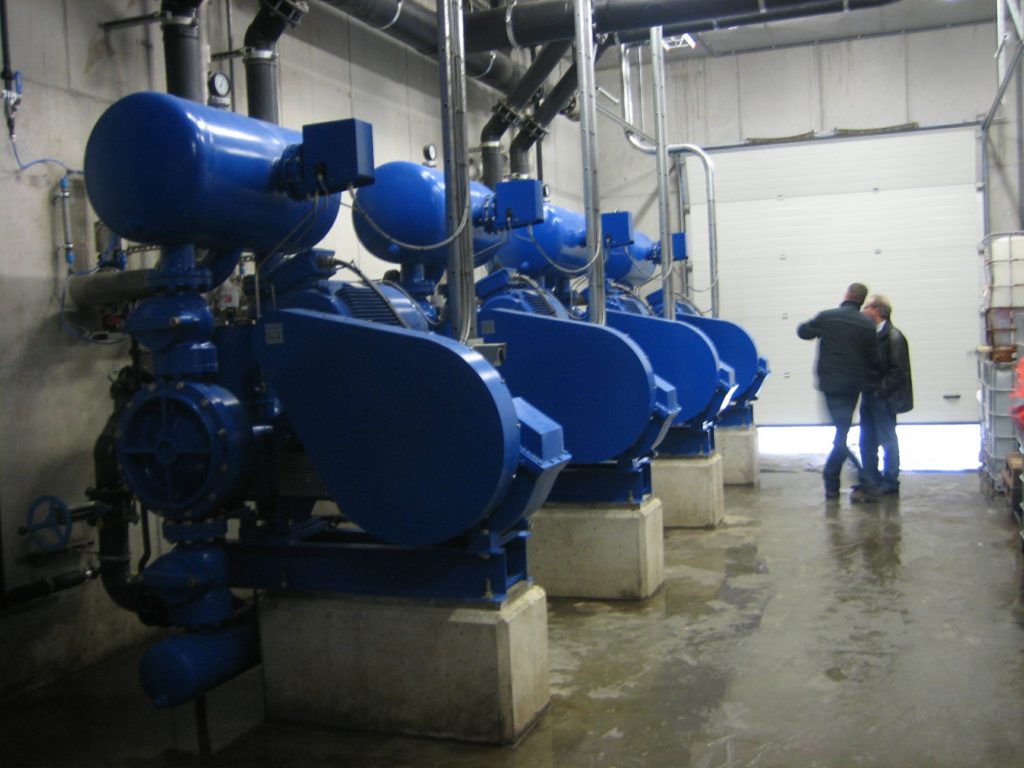
Type SP537N, 1 cylinder, double acting, 60 m³/h (264 gpm), 16 bar (232 psi), Filter Press Feeding
washing / filtration of contaminated upper layer of earth / Netherlands
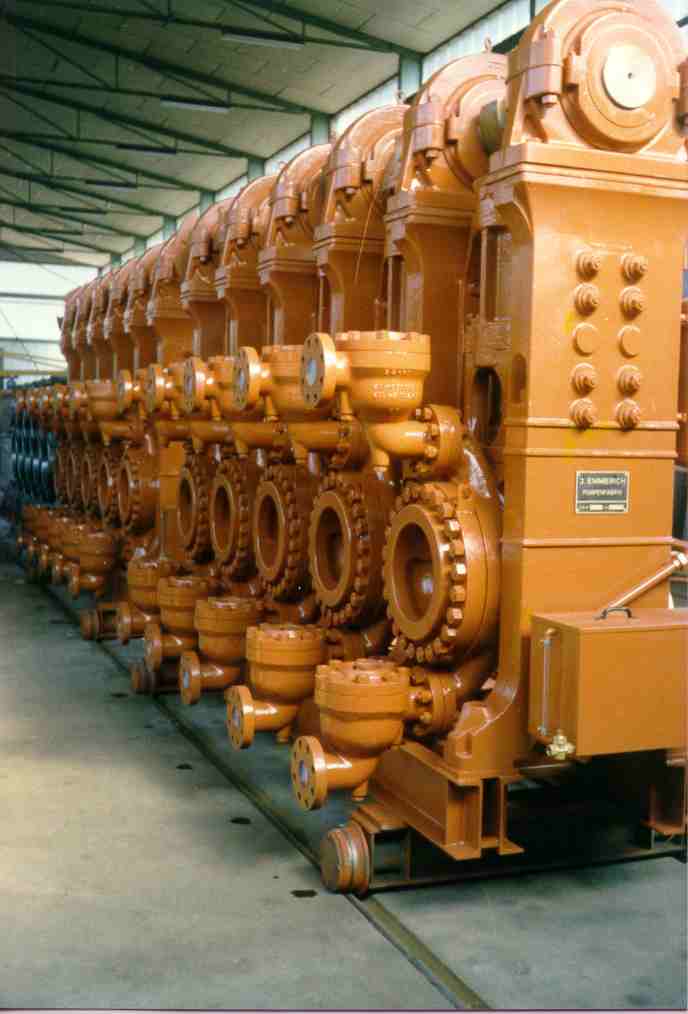
Type KM215A, 12 cylinder, single acting, 327 m³/h (1440gpm), 121 bar (1755 psi), hydraulic transfer
Aluminium / Red mud / China

Type SP520SPPH, 1 cylinder, double acting, 12 m³/h (53 gpm), 16 bar (232 psi), Filter Press Feed Pump
Al – hydroxide sludge in galvanizing plant / Germany
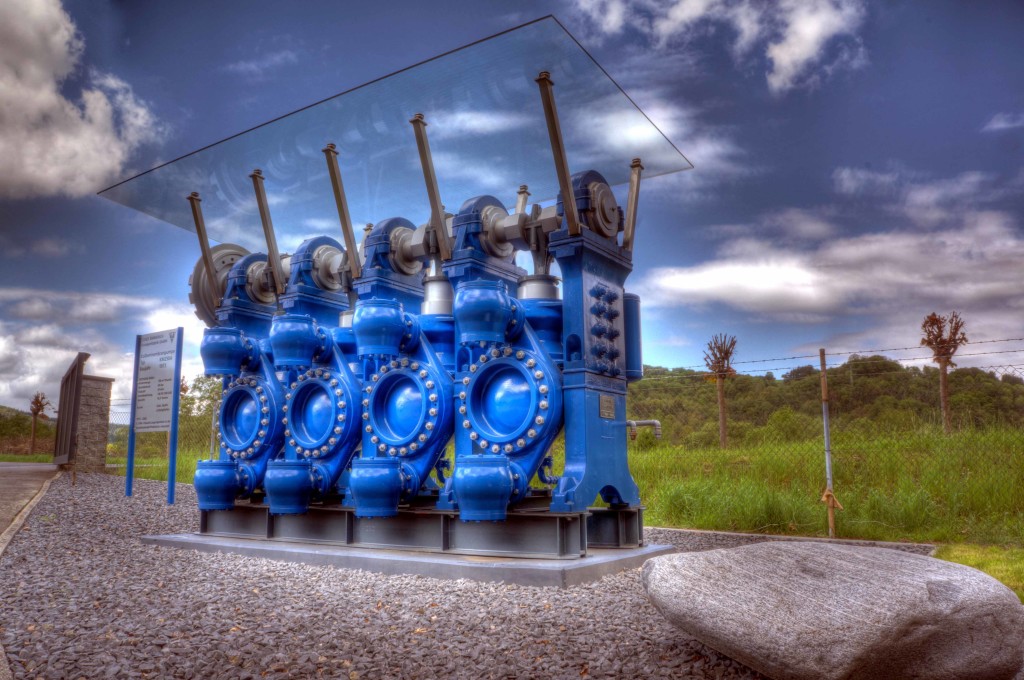
Big Blue at the Emmerich Factory
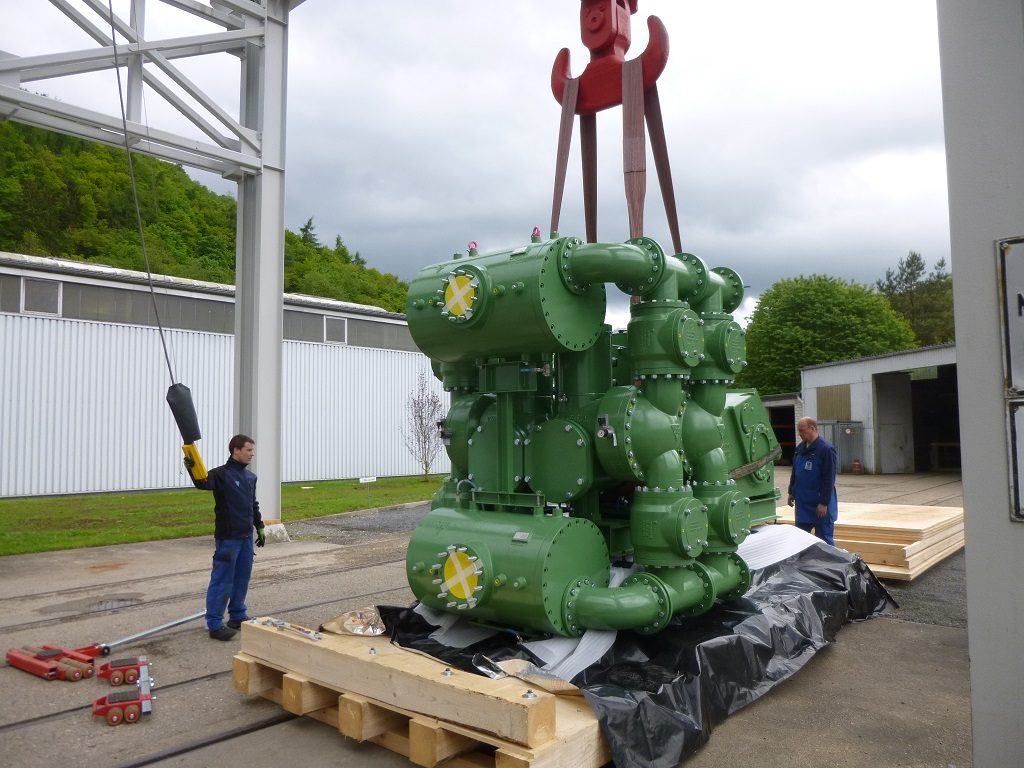
Piston Membrane Pump Being Crated for Shipment
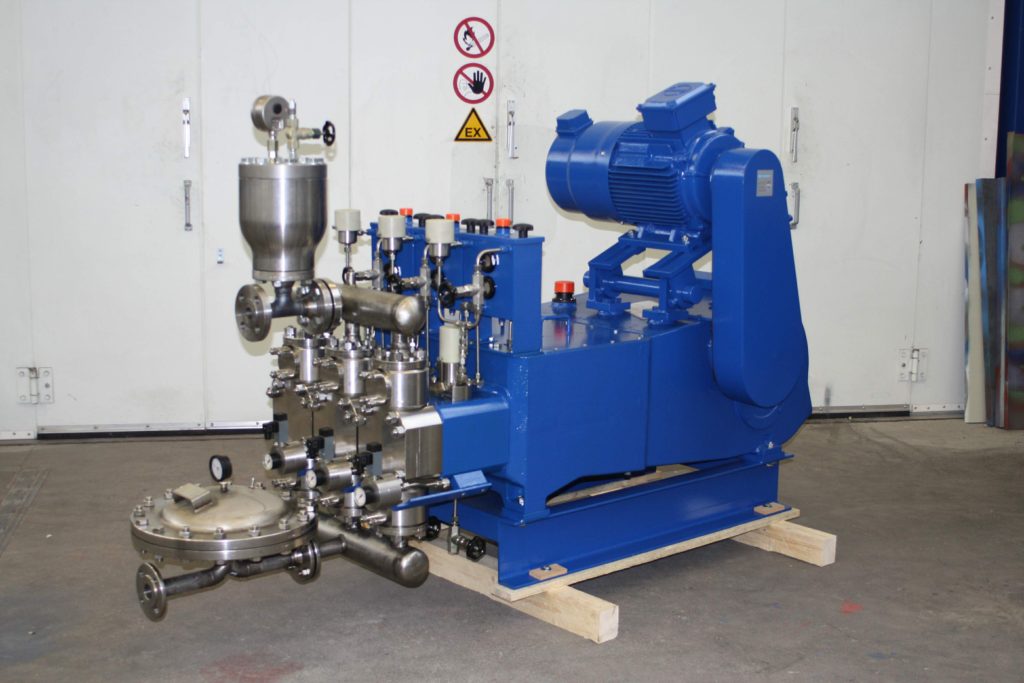
Type TKM500HD, 3 cylinder, single acting, 6 m³/h (26 gpm), 80 bar (1160 psi), hydraulic transfer
Milk of lime, Ca (OH)² / Germany
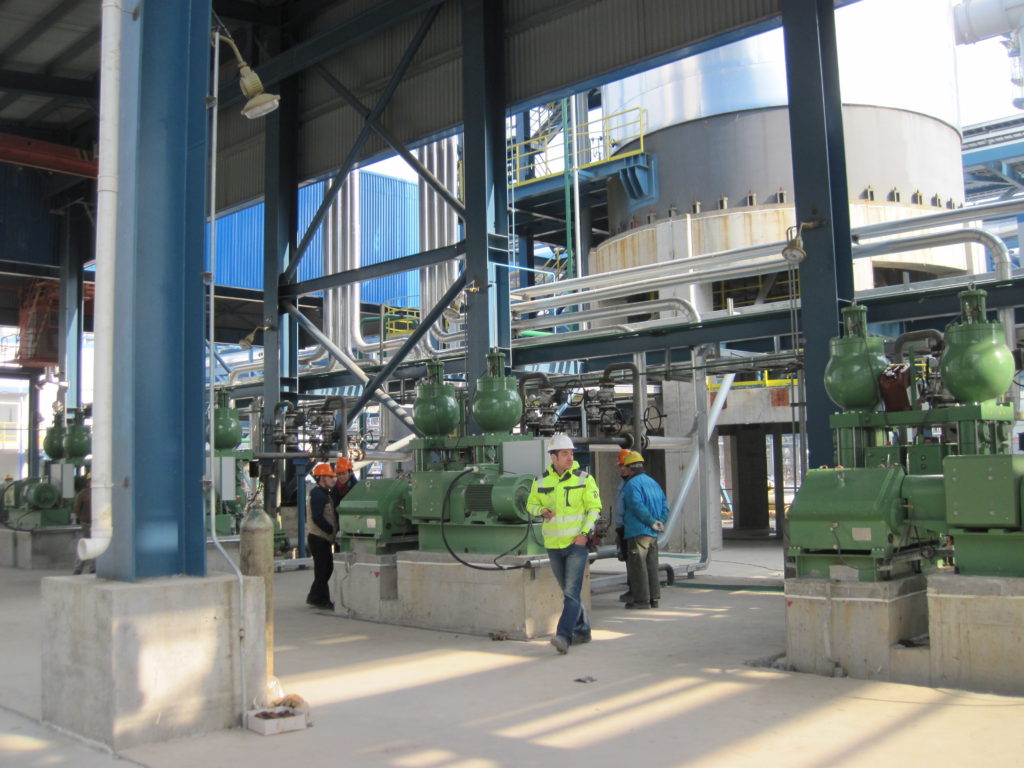
Type ZDKM500R, 2 cylinder, double acting, 30 m³/h (132 gpm), 40 bar (580 psi), hydraulic transfer
coal sludge, power plant / China
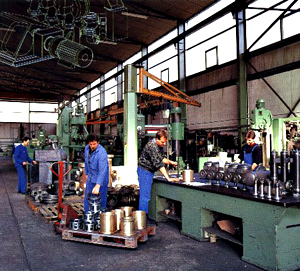
Parts Quality Control Station
Design and manufacture of pumps are by means of state of the art processes and certification to DIN ISO 9001 guaranteed quality. Product development is formed by innovative design and material technology utilizing individual customer requirements.

Pump Testing Facility
All manufactured pumps are checked on the processor controlled test stand. Automatically recorded reports of performance are provided to the customer.